INSULATION FOAM CUTTING MACHINES
Polycut is an engineering company that produces bespoke machines for the purposes of cutting insulation foam, such as polystyrene, PIR foam. This includes products such as: Kingspan Kooltherm, Kingspan Thermoroof, Celotex insulation boards, Recticel Eurothane & IKO Enertherm.
About Polycut
Polycut has been trading since 1999 and has provided hundreds of bespoke machines to customers around the world. Using the latest CAD packages and our extensive engineering experience, your exact specification can be visualised before manufacture. Our machines are manufactured and assembled in the UK in our purpose built factory. The control system is provided by Lenze, which have support teams in offices across the globe.
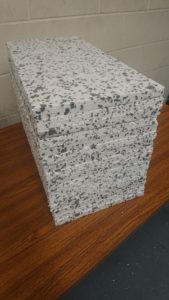
Dust Free cutting
The machine cuts the product with a specially designed, fixed knife blade so there is no dust created during the cut. The alternative method of cutting using a wall saw or reciprocating blade creates considerable dust and swarf particles, which requires extraction and cleaning.
Using the Polycut machine means that the products can be cut and used immediately, without any time consuming cleaning required.
The alternative method of cutting insulation using a rotating or reciprocating saw blade produces considerable amounts of dust during the cut and operators need to protect themselves with PPE. This is not necessary with the Polycut machine and the cut is clean.
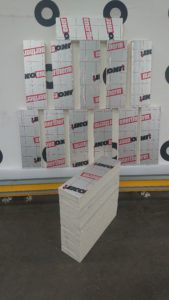
Efficient and versatile cutting
The machine is a CNC controlled robot, programmed by a suite of user friendly and powerful software. This software can be used to create quick straight cuts by the operator at the machine, or can be used to create a whole variety of different shapes, which can be nested together to optimise the usage of your stock sheets. The machine will then automatically cut all the panels at once from the whole sheet. This process takes just a few minutes to complete.
The machine can cut any straight edged shape, from rectangles, triangles, pentagons etc. It can also cut curves if required.
Running at 1.5 metres per second, the machine is capable of processing hundreds of panels per day.
The machine can also be programmed to cut the remaining stock sheet into small pieces that are easier to dispose of.
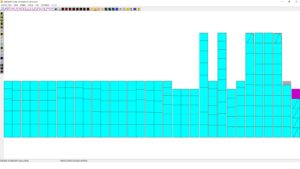
Software features
The machine employs a JWSHAPE, a feature rich optimising software package. Using this software, the operator selects the shape of panel that they want to cut from a library of over 100 different shapes.
All of the panels requiring to be cut that day can be entered in advance, and the software
will batch them together according to panel thickness/type. These batches can then be optimised automatically into cut jobs, and the CNC files produced.
These can be transferred to the machine via the network. Along with the CNC files, a supporting report is produced by the software detailing for the operator which CNC file to select, which type and size of panel to cut and a drawing showing the cut plan. Labels for each job and each panel within the job can be produced too.
Finally, a summary report is produced showing the totals for all the jobs in the batch, including sheet usage and wastage rates.
The software can be used to produce labels for the panels that are cut, which includes data such as job reference, panel dimensions, customer, and other customisable data. A label can be also be automatically generated for any offcuts that are to be retained, detailing their size and a reference.
Precision cutting
The positioning accuracy of the machine is within a tolerance of less than 1mm. A high pressure vacuum bed ensures the sheets are clamped securely during the cutting, and sacrificial stops provide a secure base for the material to ensure accurate cutting.
The knives are custom made to suit the Polycut machine, and have a long life due to the hardening process undertaken. Different knives can be used for different materials to optimise the cut quality.
A knife change tool is supplied with the machine, so that it can be changed quickly and safely – less than 5 minutes.
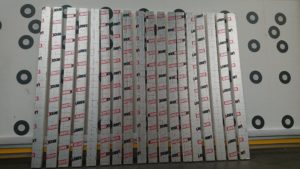
High Volume cutting
Further to cutting any type of shape from the stock sheet, the machine can also cut rectangles from multiple sheets at once, therefore significantly increasing your productivity. The standard 70mm blade provides scope for cutting several thinner sheets vertically and horizontally at the same time.
Longer blades can be made available for cutting thicker products.
To improve optimisation, several sheets can be placed on the bed at once and treated as one in the software. This gives the optimiser more scope to improve the layout of the panels you are cutting, thus reducing the wastage, saving material and money. The machine, as standard, can be loaded with up to six 2400mm x 1200mm sheets at the same time.
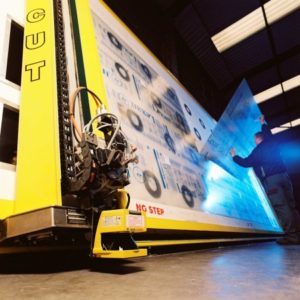
Safe operation
The machine is fitted with safety scanner at the bottom of the cutting bridge. This provides a 1.5m protection zone around the moving element at all times. If anyone strays into this zone while the machine is cutting, it is immediately halted. Once the person or object is removed from the safety zone, the machine automatically resets and the job can be resumed.
Emergency stop buttons are also present on the machine allowing the operator to immediately halt production.
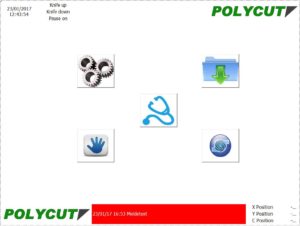
User Friendly Interface
The interface is a Windows 10 operating system with a 15” touch screen control panel. It is comprised of intuitive icons to select the various operations.
The language of the operating screens can also be changed by selecting the desired one from the setting page.
Datum calibration can be carried out from the operator screen, but is protected by password so that it cannot be accidently changed by unauthorised users.
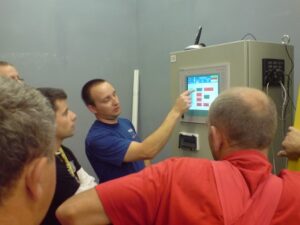
After Sales Servicing
Our in-house team of engineers are on hand to provide support after your purchase. We offer three levels of servicing packages:
Firstly you can have adhoc service requests;
Secondly we can offer annual service plans that include service visits and remote support cover during the working week;
Thirdly we offer the former, but with additional performance monitoring software.
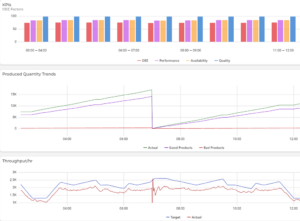
Performance Monitoring
Our third level service package includes performance monitoring of the machine.
We will continuously monitor your machine performance and can plan preventative maintenance visits to minimise the risk of unexpected downtime.
We can also provide information for you to use in assessing production performance over time.
Technical Specification
Insulation Foam Cutting Machine
The Polycut machine is manufactured to order and can be configured to suit your particular needs.
This includes changing the bed size for different sizes of sheets, changing the depth of the cut, or even just changing the colour to suit your corporate brand.
Technical details:
Standard Dimensions:
Overall Width: 1.5mtrs – Overall Length: 9.1mtrs – Overall Height: 3.2mtrs
Max linear speed: 1.5mtrs/sec
Cutting speed: Variable
Cutting head: Heavy-duty precision blade manufactured from hardened steel
Knife cutting depth: Up to 70mm
Multi-sheet or single sheet cutting? Single or Multiple
Complex shape cutting? Yes
Tolerances: +/- 0.05% of distance travelled
Overall travel of X-axis: 7.2mtrs
Overall travel of Y-axis: 2.4mtrs
Vacuum: Pressure sensitive vacuum system
Vacuum distribution: 60 vacuum points capable of being selected manually by operator or automatic switching by machine
Motion control system: Integrated PLC running pre-programmed CNC software controls & motors, which drive the cutting head. The data is supplied from a bespoke optimising package.
Optimising software: Allows the batching of any number of panels into one job, which can then optimised in seconds into the stock sheet sizes using a variety of automatic optimising algorithms. This minimises the percentage of wastage, improving efficiency and reducing time to process.
Remote diagnostics: Network internet access allows the machine to be connected to our engineering office, providing status data and facilitating online support and training.
Knife changing from the front
Knife changing from the rear
Multicut Polycut | ||
Knife cutting depth | Up to 70mm | |
Multi-sheet or single sheet cutting? | Single or Multiple | |
Complex shape cutting? | Yes |
How To Purchase
Please contact us to request a full quotation and specification on any of the machines. Once an order is placed, your production slot will be allocated, and manufacture will commence.
The machines are produced to order, and the lead times vary depending on the machine specification and the availability of components at that time.
Lead time will be confirmed following order.
Installation
Installation usually takes 1 day as your machine will be delivered fully assembled.
Our inhouse team of engineers will carry out servicing work on the machines over their life and maintenance packages are available. This includes remote support via telephone or web based connection direct to the machine for updates, training or support.
The only consumable items on the machine are the blades, and the sacrificial felt covering on the cutting bed. All of these items are available ex stock from our factory.
Keep in Touch
Unit 2 Sidings Business Park, Freightliner Road, HULL HU3 4XA, UK
Tel: +44 (0) 1482 221821 email: mark@polycut-uk.com whatsapp: +44 (0)7985 522367